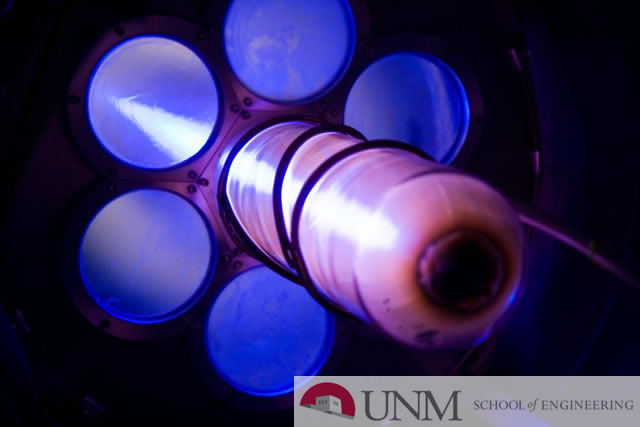
Mechanical Engineering ETDs
Publication Date
3-7-1967
Abstract
In the field of research and development and the growing area of environmental testing a good method of measuring compressive forces, often under the most adverse field conditions, has been sought many times over. Several methods, both direct and indirect, have been used to attempt to define such compressive loads. Some are universally successful, but often a method has to be developed for each individual job.
A common problem among existing force transducers is their delicacy and mortality rate under field conditions. Some are complex and costly, and repeated replacement of damaged units is quite undesirable. Many transducers that are satisfactory in closely controlled laboratory tests, are unusable when field assembly is required because precision fitting and assembly are impossible. Often the data reduction or data analysis required by commercial transducers and individual developments alike are rather extensive and may become prohibitive. Any addition to the selection of special purpose force measuring -devices, if truly effective, could find many opportunities for service.
The compressive force transducer developed in this project is intended to relieve or minimize some of these problems. It was specifically designed for determining the lateral dynamic input loads on a high velocity, dual rail rocket sled. The design concept, however, may be adapted to a wide variety of load capacities and physical dimensions permitting use in different applications.
The transducer would find use in applications whenever knowledge of compressive forces is required under field conditions, which subject the transducer to abuse from rough handling, and unknown load distributions and directions of applied force.
The goal of this study was to develop a force transducer prototype that had the following characteristics:
1. Rugged construction--so that the structure of which the transducer is a part or to which it is attached could be assembled by unwieldy handling equipment without damaging the transducer, and, so that the transducer is undamaged by any type of load application as long as the magnitude is within the capacity of the transducer.
2. Uneffected by varied load distributions-capable of accurate load measurement even though they are not applied directly along the sensitive axis of the transducer. This type of load could be caused either by the nature of the load or as a result of improper mounting.
3. Simple inexpensive construction--avoiding elaborate, complex design which would be difficult, lengthy, and costly to fabricate.
4. Linear calibration--so that read-out and data analysis would be a minimum.
5. Universal application--adaptable to different test structures with minimum modification.
6. Static and dynamic capabil1ties--with a frequency range from DC to approximately 200 Hertz.
With these general objectives defined, a discussion of the specific problem is now presented.
Degree Name
Mechanical Engineering
Level of Degree
Masters
Department Name
Mechanical Engineering
First Committee Member (Chair)
William Ernest Baker
Second Committee Member
Richard Charles Dove
Third Committee Member
Arthur Vincent Houghton III
Fourth Committee Member
James Vernon Lewis
Document Type
Thesis
Language
English
Recommended Citation
Workhoven, Robert Merrill. "A Compressive Force Transducer For Use On Rocket Sleds.." (1967). https://digitalrepository.unm.edu/me_etds/269