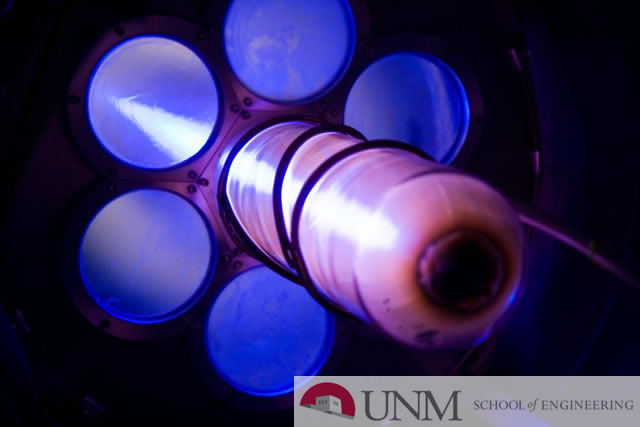
Mechanical Engineering ETDs
Publication Date
7-18-1978
Abstract
Prediction of pressure and leakage in a hydrodynamic bearing when surface roughness effects are important is an essential step in bearing design. The inclusion of surface roughness effects in bearing analysis allows more accurate prediction of bearing life. It has been shown that the average flow model developed by Cheng and Patir is a promising technique for determining surface roughness effects. The objective of this investigation is to examine the validity, applicability and limitation of the average flow model. Validity of the average flow model is ascertained by checking the independence of flow factors. Discussion of the general Reynolds equation for rough surfaces, which is the starting point for the flow model, delineates the applicability of the technique. Limitations of the model are found by studying the effects of physical interpretation, boundary conditions, choice of surface roughness function and selection of numerical method on the average flow results. A numerical method which differs from that used by Patir and Cheng, termed the corner point method, is developed and is considered as an alternative representation of the rough surface lubrication. This method predicts flow in a two-dimensional rough bearing segment given the nominal film thickness, surface velocity components and boundary conditions. The validity of the corner point method is verified by two independent sources. Using the corner point method, the validity of the average flow hypothesis is verified. However, the results for flow factors are found to be boundary dependent, imposing a restriction on the applicability of the average flow model. It is also found that the results depend on relative asperity to bearing segment size, indicating that the average flow model requires more work before it can be applied to bearing design. Finally, it is observed that flow factor results are extremely dependent on the choice of a rough surface distribution function. A truncated roughness distribution is assumed which is considered a better physical and mathematical approximation to real surfaces than the Gaussian symmetric distribution used in previous research. Results for this surface indicate that the truncated surface is characterized by a lower resistance to flow than the symmetric surface.
Degree Name
Mechanical Engineering
Level of Degree
Masters
Department Name
Mechanical Engineering
First Committee Member (Chair)
Alan Otto Lebeck
Second Committee Member
Richard Scott Passamaneck
Third Committee Member
Pramod Kumar Pathak
Sponsors
The Office of Naval Research contract number ONR N00014-76-C-0071
Document Type
Thesis
Language
English
Recommended Citation
Teale, Johnny Lynn. "Surface Roughness Effects in Hydrodynamic Lubrication." (1978). https://digitalrepository.unm.edu/me_etds/261