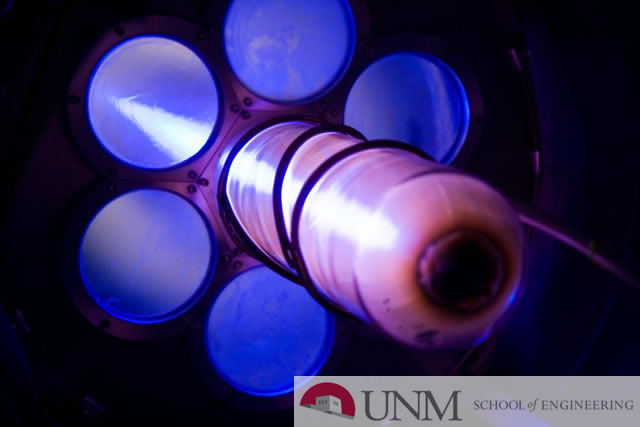
Mechanical Engineering ETDs
Publication Date
5-5-1977
Abstract
The heat transfer process for a special class of wick fed grooved heat pipe evaporators was investigated analytically and experimentally. The heat pipes studied had vapor release slots cut through the evaporator wick to enhance removal of the vapor generated in the evaporator. As a result of the slots, the liquid menisci formed between the groove tips and the transport wick rather than at the base of the grooves as normally observed. This type of heat pipe evaporator is referred to as an inverted meniscus design.
A comprehensive survey of the literature was completed to establish the existing state of knowledge on evaporator heat transfer. Emphasis was placed on research relating to the problem of removing the vapor from the evaporator without disturbing the liquid flow in the wick.
Thirty-one variations of the basic design were experimentally evaluated and the results reported. A variety of wick materials were applied to evaporators of various groove densities. Screens from 100 to 1400 mesh of various metals, copper feltmetals and composite wicks were all evaluated. Water was the working fluid in all cases.
Basic heat pipe performance relationships were expanded to include inverted meniscus designs. Predictions of the critical heat rate, temperature difference and the heat transfer coefficient were established for each heat pipe tested. The model predicted the experimental results within 10 percent.
As a result of the analytical and experimental correlation and visual observation, the meniscus position was verified and the mode of heat transfer determined. For the inverted meniscus evaporators investigated, conduction through the heat pipe wall and through a liquid layer with evaporation from the liquid surface was found to be the primary heat transfer mechanism.
The mechanism limiting the critical heat rate was found to be a capillary limit. The ability of the wick to supply sufficient fluid to the evaporator controlled the maximum heat rate. When internal pressure losses equaled the pumping head available, the critical heat rate was achieved. The theoretical model was used to predict the effect of each variable on heat pipe performance. Additionally, the potential of inverted meniscus heat pipes for laser mirror heat removal is discussed.
Degree Name
Mechanical Engineering
Level of Degree
Doctoral
Department Name
Mechanical Engineering
First Committee Member (Chair)
Karl Thomas Feldman Jr.
Second Committee Member
Charles Gilbert Richards
Third Committee Member
Arthur Vincent Houghton III
Fourth Committee Member
L. Schlie
Document Type
Dissertation
Language
English
Recommended Citation
Oliver, Richard Clarke. "Investigation of Evaporation from Grooved Inverted Meniscus Heat Pipe Wicks." (1977). https://digitalrepository.unm.edu/me_etds/175