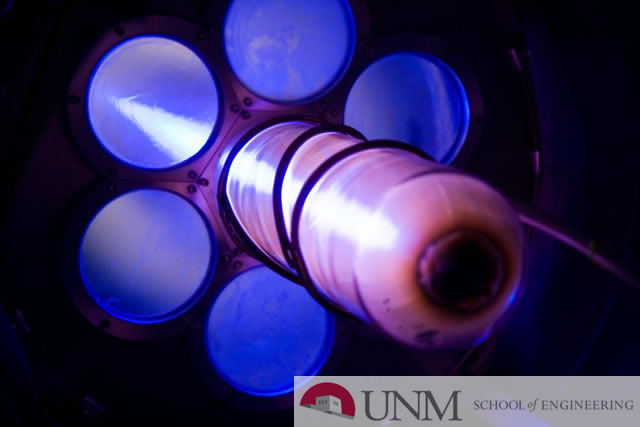
Mechanical Engineering ETDs
Publication Date
Fall 11-7-2019
Abstract
Additive manufacturing allows for the development of complex geometrical designs that may otherwise be impossible to fabricate through common methods. This advantage has opened the door to a new testing method capable of rapid and efficient material property characterization and qualification. The technique exhibits how 100’s of sub-size tensile bars can be tested to show an inherent statistical variation of materials produced by laser powder bed fusion. The testing technique presented is used to evaluate various heat treatments of the nickel super-alloy Inconel 625 and the aluminum alloy AlSi10Mg after stress relief annealing. Statistical analysis using 3-parameter Weibull distributions is used to determine low-probably extreme values of both material’s mechanical properties. Abnormally low ductility values of hot isostatic pressed Inconel 625 are determined to be due to the presence of large carbides along grain boundaries, characterized by electron dispersive spectroscopy (EDS). Incorrect processing parameters lead to the formation of lack of fusion voids in the Al-alloy, significantly reducing the effective load-bearing cross-sectional and triggering premature failure.
Degree Name
Mechanical Engineering
Level of Degree
Masters
Department Name
Mechanical Engineering
First Committee Member (Chair)
Dr. Yu-Lin Shen
Second Committee Member
Dr. Tariq Khraishi
Third Committee Member
Dr. Jay Carroll
Document Type
Thesis
Recommended Citation
Robbins, Aron. "Mechanical Characterization of Additively Manufactured Inconel 625 and AlSi10Mg via High-Throughput Tensile Testing." (2019). https://digitalrepository.unm.edu/me_etds/177