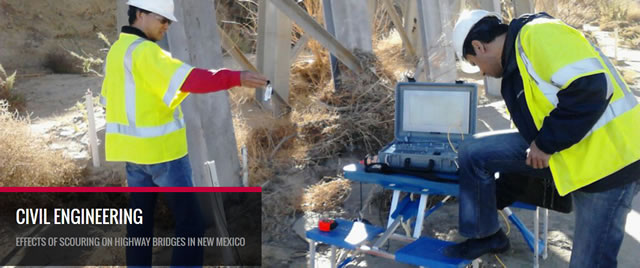
Civil Engineering ETDs
Publication Date
Spring 5-20-2022
Abstract
Elastomeric materials are extensively used in energy dissipation applications to mitigate large lateral displacements and attenuate vibrations. One way of exploiting the capabilities of elastomeric materials is using shear-damping mechanisms such as viscoelastic damping devices (VEDs).
In this research the freedom of design offered by additive manufacturing technology is utilized to produce 3D printed elastomeric parts that act as the viscoelastic layer in an energy damping device. A mechanically interlocked viscoelastic damper (MIVED) with a jigsaw-like interlocking mechanism was designed and manufactured. MIVED is composed of a rigid and soft phase. It operates in two modes, modes I and II, that depend on the stiffnesses of the rigid and soft phases as well as the stiffness of the connection used to fix it to the testing machine or structural element. The modes are illustrated through changing the rigid and soft phase materials. For that purpose, two devices were fabricated MIVED-1 and MIVED-2 to observe modes I and II, respectively. The rigid phase of MIVED-1 was made of steel, while the soft phase is 3D printed using vi thermoplastic polyurethane (TPU). MIVED-2 had a rigid phase made from 3D printed fiber reinforced nylon, and 3D printed TPU injected with silicone rubber for the soft phase.
The devices were cyclically tested under different amplitudes and frequencies, and the response was examined. 3D printed TPU was mechanically characterized using uniaxial cyclic tension tests under different rates and different printing processing parameters. Stress relaxation tests were also conducted to obtain the viscoelastic behavior of the TPU material. Material characterization of TPU was used to develop a finite element (FE) model that is used to simulate the mechanically interlocked damper. The FE model was validated with the experimental observations of TPU specimens and MIVED-1 and was then used to examine the significance of damper geometry and material parameters on the efficiency of energy dissipation using the 3D printed interlocking mechanism.
Finally, the performance of the device was evaluated as a part of a structural frame system. A simplified analytical model of the device was developed and incorporated within the frame system. The frame was then subjected to El Centro ground acceleration and the response of the structural system was studied.
Keywords
Energy dissipation, Topological interlocking, 3D-printed dampers, Hyperleastic, Fused deposition modeling
Document Type
Dissertation
Language
English
Degree Name
Civil Engineering
Level of Degree
Doctoral
Department Name
Civil Engineering
First Committee Member (Chair)
Mahmoud Reda Taha
Second Committee Member
Yu-Lin Shen
Third Committee Member
Fernando Moreu
Fourth Committee Member
Eslam Soliman
Recommended Citation
Jaradat, Mohammed. "Experimental and Numerical Investigation of 3D-Printed Viscoelastic Dampers." (2022). https://digitalrepository.unm.edu/ce_etds/260