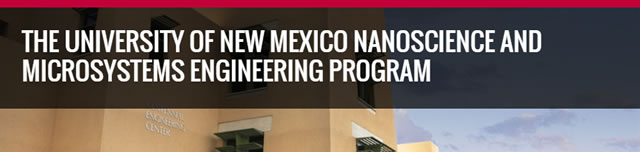
Nanoscience and Microsystems ETDs
Publication Date
Spring 4-15-2019
Abstract
Nanopatterns found in nature demonstrate that macroscopic properties of a surface are tied to its nano-scale structure. Tailoring the nanostructure allows those macroscopic surface properties to be engineered. However, a capability-gap in manufacturing technology inhibits mass-production of nanotechnologies based on simple, nanometer-scale surface patterns. This gap represents an opportunity for research and development of nanoimprint lithography (NIL) processes. NIL is a process for replicating patterns by imprinting a fluid layer with a solid, nano-patterned template, after which ultraviolet cure solidifies the fluid resulting in a nano-patterned surface. Although NIL has been demonstrated to replicate pattern features as small as 4 nm, there are significant challenges in using it to produce nanotechnology. Ink-jet deposition methods deliver the small fluid volumes necessary to produce the nanopattern, and drop volumes can be tuned to what the pattern requires. However the drops trap pockets of gas as they merge and fill the template, and due to relatively slow gas dissolution, reduce processing throughput. Capillary forces that arise from the gas-liquid interfaces drive non-uniform gap closure and the resulting variations in residual layer reduces process yield or degrades product performance.
This thesis develops reduced-order models for fluid flow and structural mechanics of the imprint process for NIL. Understanding key phenomena of gas trapping and residual layer non-uniformity drives model development to better understand how throughput and yield can be improved.
Reynolds lubrication theory, the \textit{disperse} type of multiphase flow, and a lumped-parameter model of dissolution unite to produce a two-phase flow model for NIL simulations of 10,000 drops per $\text{cm}^2$. Qualitative agreement between simulation and experiment provides a modicum of validation of this model for flow in NIL simulations. The two-phase model simulations predicts that both dissolution and viscous resistance affect throughput.
The coupling of a reduced-order model for 3D structural mechanics with the two-phase flow model enables simulations of drop merger on a free-span tensioned web. Challenges in improving the structural model lead to formulation of a 2D model for which sources of instability are more easily discovered and understood. Inextensible cylindrical shell theory and lubrication theory combine into a model for the elastohydrodynamics of a rolling-imprint modality of NIL. Foil-bearing theory describes the lubrication layer that forms between a thin, tensioned web moving past another surface. Reproduction of the results of foil-bearing theory validates this coupled model and reveals a highly predictable region of uniformity that provides low shear stress conditions ideal for UV-cure. These results show theoretical limitations that are used to construct a processing window for predicting process feasibility.
Keywords
nanoimprint lithography, Reynolds lubrication, multiphase, cylindrical shell, foil bearing
Sponsors
National Science Foundation
Document Type
Dissertation
Language
English
Degree Name
Nanoscience and Microsystems
Level of Degree
Doctoral
Department Name
Nanoscience and Microsystems
First Committee Member (Chair)
P. Randall Schunk
Second Committee Member
Peter Vorobieff
Third Committee Member
Dimiter Petsev
Fourth Committee Member
Roger T. Bonnecaze
Recommended Citation
Cochrane, Andrew. "Modeling multiphase flow and substrate deformation in nanoimprint manufacturing systems." (2019). https://digitalrepository.unm.edu/nsms_etds/51
Included in
Engineering Physics Commons, Fluid Dynamics Commons, Nanoscience and Nanotechnology Commons