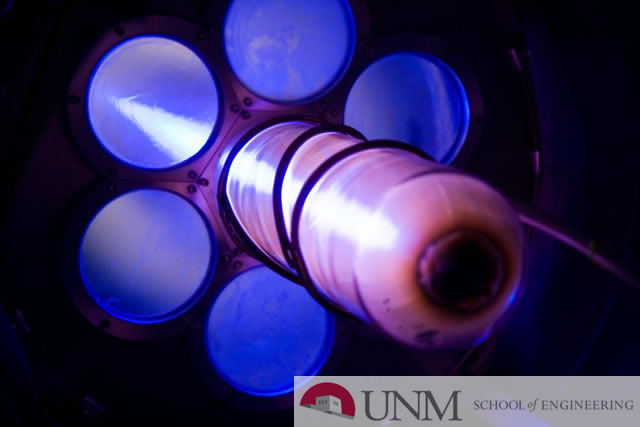
Mechanical Engineering ETDs
Publication Date
2-1-2012
Abstract
Carbon fiber composites are of significant interest for use in deployable space structures. Elastically folded thin laminates can be utilized as hinge mechanisms in structural systems such as solar arrays, reflectors, and instrument booms, allowing for compact packaging during launch to orbit. While the initiative to utilize composite laminates in deployable structures has increased it also has faced difficulties in design and analysis of these poorly understood materials. Data from standardized ASTM test methods fails to characterize nonlinear constitutive behavior over the full large strain range common to deployable structures. Flexural behavior is characterized by the moment vs. curvature response therefore requiring a bending test. A special test fixture is developed to allow flexural testing of thin plates at large strains. Reaching large strains during the test provides an opportunity to investigate the large strain linear and nonlinear elastic constitutive behavior of glass and carbon fibers respectively. A flexural test campaign was carried out for three unidirectional continuous fiber reinforced plastic materials in a large deformation four point bending fixture. Intermediate and high modulus PAN and S2 fibers were tested because they are commonly used in deployable structures. The fixture is designed to apply load, which through translation and rotation of wheeled carts, induces a pure moment in the sample. We utilize a previously developed first order nonlinear empirical constitutive model to represent fiber axial tensile and compressive behavior and rule of mixtures with a linear matrix model for laminate behavior. We use algorithms for nonlinear curve fitting of moment-curvature response measured using the test fixture and fit for a nonlinear constitutive parameter and fiber volume fraction. Using previously reported nonlinear tension parameter for IM7 fiber of 21.4 we estimated for the fibers nonlinear compression parameter to be γ_C=20.7. For test data of S2 fiberglass made by A.G.Y. and M55J carbon fiber made by Toray® the fit model did not differentiate between nonlinear constitutive parameter in tension or compression. Analysis of the experimental data returned a large nonlinear constitutive parameter of 97.6 for M55J fiber and a small nonlinear constitutive parameter of 6.7 for S2.'
Keywords
Laminated materials--Fatigue, Fibrous composites--Fatigue, Carbon fiber-reinforced plastics--Fatigue, Expandable space structures--Materials--Testing, Parameter estimation.
Degree Name
Mechanical Engineering
Level of Degree
Masters
Department Name
Mechanical Engineering
First Committee Member (Chair)
Shen, Yu-Lin
Second Committee Member
Murphey, Thomas
Document Type
Thesis
Language
English
Recommended Citation
Grigoriev, Mikhail. "Large strain flexural testing of thin composite laminates." (2012). https://digitalrepository.unm.edu/me_etds/53