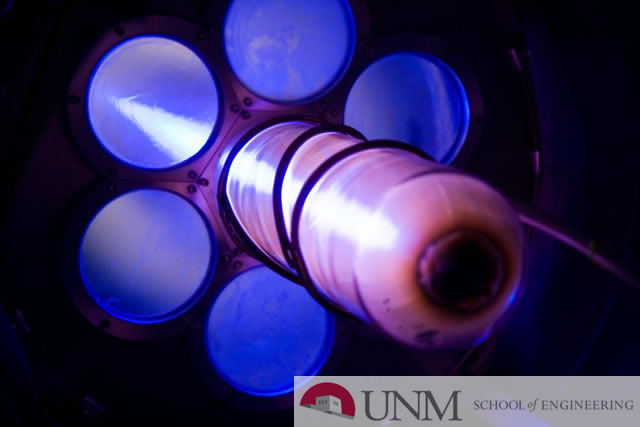
Mechanical Engineering ETDs
Publication Date
2-9-2010
Abstract
A numerical study was undertaken to investigate the solder joint failure under fast loading conditions. The finite element model assumes a lap-shear testing configuration, where the solder joint is bonded to two copper substrates. A progressive ductile damage model was incorporated into the rate-dependent constitutive response of the Sn (tin)-Ag (silver)-Cu (copper) solder alloy, resulting in the capability of simulating damage evolution leading to eventual failure through crack formation. Attention is devoted to deformation under relative high strain rates (1-100 s-1), mimicking those frequently encountered in drop and impact loading of the solder points. The effects of applied strain rate and loading mode on the overall ductility and failure pattern were specifically investigated. It was found that the solder joint can actually become more ductile as the applied strain rate increases, which is due to the alteration of the crack path. Failure of the solder is very sensitive to the deformation mode, with a superimposed tension/compression on shear easily changing the crack path and tending to reduce the solder joint ductility. In addition, cyclic shearing resulted in different failure patterns from those of monotonic loading. The two fatigue cracks, one at (or very close to) each interface, have both grown to a significant length with one responsible for final failure of the joint.
Keywords
Solder and soldering--Cracking--Mathematical models, Joints (Engineering)--Fatigue--Mathematical models, Materials--Dynamic testing--Mathematical models, Finite element method.
Degree Name
Mechanical Engineering
Level of Degree
Masters
Department Name
Mechanical Engineering
First Committee Member (Chair)
Leseman, Zayd
Second Committee Member
Luhrs, Claudia
Document Type
Thesis
Language
English
Recommended Citation
Aluru, Kiranmaye. "Numerical study of solder joint failure under fast loading conditions." (2010). https://digitalrepository.unm.edu/me_etds/40