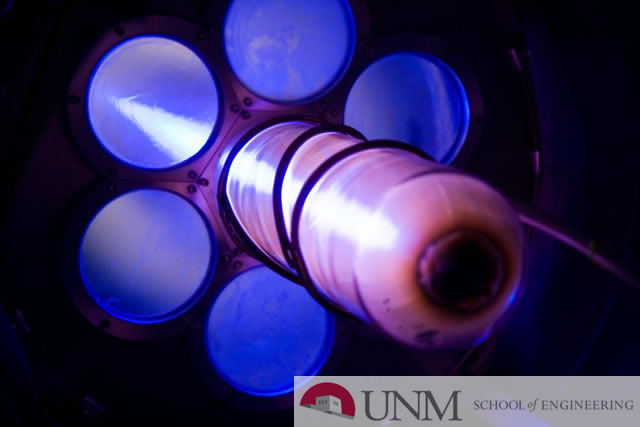
Mechanical Engineering ETDs
Publication Date
5-1978
Abstract
A desirable objective of mechanical face seal design is to achieve the maximum hydrodynamic load support possible while maintaining an acceptable leakage. In this way, mechanical face seal life can be greatly extended as the wear of the seal faces is significantly reduced. It has been shown that circumferentially varying waviness of one of the faces of a mechanical face seal causes such hydrodynamic lubrication.
The objective of this investigation is to examine the performance characteristics of the wavy mechanical face seal by studying the effects of certain design parameters. Seal performance is measured by leakage and wear rate. The design parameters investigated are seal face width, surface roughness, the number of waves around the seal face, the shape and amplitude of the waviness, and ring stiffness.
A previously developed numerical model is used as the basis for the present investigation. The model is a two-dimensional approximation that accounts for the effects of hydrodynamic and hydrostatic pressure, fluid film cavitation, surface roughness, and asperity contact and load support. The fraction of the load supported by fluid pressure, pressure distribution, coefficient of friction, and face seal leakage are predicted given the parameters which include waviness amplitude, number of waves, sealed pressure, rotating speed, material properties, face seal geometry, viscosity, and surface roughness.
The parameter studies show that the most important design parameters influencing seal performance are surface roughness and waviness amplitude. An optimization routine is used to determine the wave shape that results in maximizing the hydrodynamic effects while maintaining a prescribed leakage. The results show that the simple cosine wave shape is optimum.
The design parameter study results are examined considering the physical limitations that exist in face seals. It is seen that there are stability problems that must be considered when designing a wavy face seal. It is shown that surface roughness values low enough to allow hydrodynamic lubrication exist in present mechanical face seals. Recommendations are made to improve face seal performance as a function of the design parameters.
A procedure to be used in designing a wavy mechanical face seal is developed. Using this procedure on a typical face seal, a reduction in the seal face wear rate of 17:l was obtained compared to an identical face seal without waviness.
Degree Name
Mechanical Engineering
Level of Degree
Masters
Department Name
Mechanical Engineering
First Committee Member (Chair)
Alan Otto Lebeck
Second Committee Member
Gregory Paul Starr
Third Committee Member
William Ernest Baker
Document Type
Thesis
Language
English
Recommended Citation
Pierce, Raymond Edward. "A Design Study For A Wavy Hydrodynamic Mechanical Face Seal." (1978). https://digitalrepository.unm.edu/me_etds/249