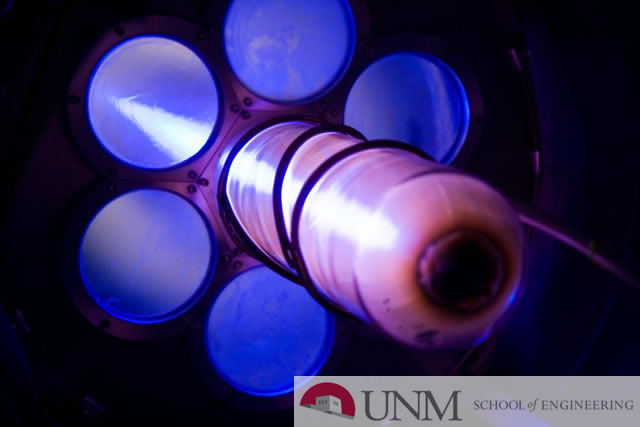
Mechanical Engineering ETDs
Publication Date
7-2-2013
Abstract
Many MEMS devices utilize nanocrystalline thin metallic films as mechanical structures, in particular, micro switching devices where these films are used as Ohmic contacts. But the elastic and plastic properties of these thin films (thickness < 1μm) are significantly different from those of the bulk material. At these scales the volume fraction of material defects such as: grain boundaries, dislocations and interstitials become quite significant and become a chief contributor to the physical and mechanical material properties. In order to effectively design MEMS devices it is important that these material properties are explored and mechanical behavior of the structure they form be characterized. Popular thin film materials used in MEMS devices are Aluminum (Al), Copper (Cu), Nickel (Ni) and Gold (Au). Platinum has traditionally gained acceptance into the MEMS industry because of its chemical inertness and high temperature stability. However the mechanical properties of platinum remains the least exploited. Platinum has a high Youngs Modulus (164 GPa, for bulk) and high melting temperature (1768 oC) and therefore can be used as a 'thin film' structure (cantilever, a bridge or a membrane) in high temperature environments with high resistance to mechanical failure. The physical size of these thin film structure make it very difficult to handle them and employ traditional mechanical testing methodologies and techniques and therefore require custom test platforms. One such recently developed platform is presented in this dissertation. The test platform is comprised of a microfabricated cascaded thermal actuator system and test specimen. The cascaded thermal actuator system is capable of providing tens of microns of displacement and tens of milli-Newton forces simultaneously while applying a relatively low temperature gradient across the test specimen. The dimensions of the platform make its use possible in both the SEM/TEM environments and on a probe station under an optical microscope. Digital image correlation was used to obtain similar accuracy (~10 nm) for displacement measurements in both an SEM and under an optical microscope. The mechanical behavior of nanocrystalline thin film structure has been the subject of extensive research in recent years. Mainly, the focus has been on the effects of the film thickness with only a few researchers mentioning anything about the grain sizes of their polycrystalline films. The effect of thin film cross sectional morphology on the mechanical behavior of a thin film structure has never been studied directly. Presented in this dissertation is experimental evidence that these thin film structures are composite structures of various grain morphologies and the overall mechanical behavior exhibited by them is the combined effect of individual contributions of each of these grain morphologies.'
Keywords
Metallic films--Mechanical properties--Testing, Platinum--Mechanical properties--testing, Microactuators, Nanostructured materials--Testing, Microelectromechanical systems--Design and construction.
Degree Name
Mechanical Engineering
Level of Degree
Doctoral
Department Name
Mechanical Engineering
First Committee Member (Chair)
Shen, Yu-Lin
Second Committee Member
Hall, Christopher
Third Committee Member
Hossein-Zadeh, Mani
Document Type
Dissertation
Language
English
Recommended Citation
Abbas, Khawar. "Characterization of the mechanical properties of freestanding platinum thin films." (2013). https://digitalrepository.unm.edu/me_etds/17