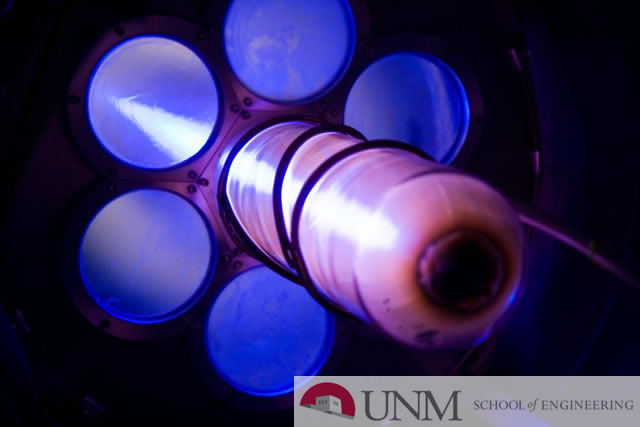
Mechanical Engineering ETDs
Publication Date
Fall 11-6-2018
Abstract
The United States Air Force is focused on reducing mass and power consumption of spacecraft to increase their capabilities for space missions. Low mass and power consumption can be achieved by using composites with low density and high stiffness and utilizing few satellite components. One way to achieve reduced mass is by eliminating attendant deployment mechanisms consuming valuable power and mass allocations on spacecraft with deployable structures. Secondary systems are typically used to assist deployable space structures to ensure 100% success. A passively deployed space structure would be of great value to the Department of Defense and the commercial marketplace. Attaining a passively deployed space structure that is reliable, predictable and controllable to tailored design applications would serve this objective.
The research presented herein was experimentally focused and involved incorporation of alumina nanoparticles (ANPs) dispersed into a three-ply composite laminate tape spring structure. The FlexLam composite was designed and fabricated for this class of tape spring deployable structures. A total of 51 tape springs were structurally tested on a unique, custom-designed test fixture with methodology to analyze their stress relaxation behavior in a coiled state for lengths of time varying from 1 hour to 6 months. A finite element model (FEM) with a Fortran subroutine was built and simulations were correlated with the structural deployment testing of 26 control tape springs and 25 ANP tape springs. The FEM simulation-predicted results correlated within 5% of the experimental testing structural results. A total of 5 epoxy samples (3 neat epoxy and 2 ANP epoxy) were fabricated and cut into 29 coupons for Dynamic Mechanical Analyzation (DMA) tests and Scanning Electron Microscope with Energy Dispersive X-ray Spectroscopy (SEM/EDS) examinations were also performed on 4 test coupons (3 ANP and 1 control) to characterize the microstructure of the composites, including the ANP dispersion and agglomeration. It was shown the ANP tape spring structures were able to retain 55% more tip force and experience less stress relaxation compared to the control tape springs. Future work is recommended in optimization of the composite and further development of the FEM simulation for improving structural behavior prediction.
Keywords
composite, deployable structure, nanoparticles, alumina, tape spring
Degree Name
Mechanical Engineering
Level of Degree
Doctoral
Department Name
Mechanical Engineering
First Committee Member (Chair)
Mahmoud Reda Taha
Second Committee Member
Yu-Lin Shen
Third Committee Member
Mehran Tehrani
Fourth Committee Member
Kawai Kwok
Document Type
Dissertation
Language
English
Recommended Citation
Scherbarth, Mark. "ENGINEERING VISCOELASTIC BEHAVIOR OF CARBON FIBER REINFORCED POLYMER COMPOSITES WITH NANOPARTICLES FOR CONTROLLING DEPLOYMENT OF AEROSPACE STRUCTURES." (2018). https://digitalrepository.unm.edu/me_etds/157