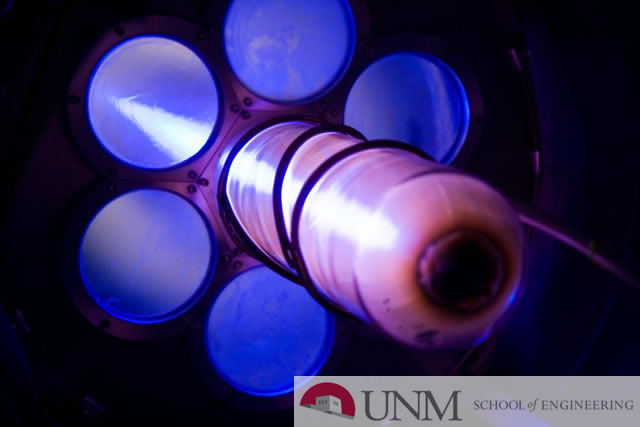
Electrical and Computer Engineering ETDs
Publication Date
Spring 5-1997
Abstract
Surface micromachined pressure sensors were designed, modeled, fabricated, and tested. They employed a piezoresistive transduction mechanism and were based upon circular diaphragms, which vary from 50 to 1000 μm in diameter and 1 to 2 μm in thickness. The piezoresistors were placed in Wheatstone bridge configurations to provide simple signal amplification and first order temperature compensation.
Of the different micromachining techniques, surface-micromachining has the advantage of being the most similar to integrated circuit manufacturing. Hence an existing IC equipment set can be used to create mechanical structures. Furthermore, the monolithic integration of a mechanical device with control electronics is simpler using surface micromachining.
Two distinct architectures of piezoresistive pressure sensors have been fabricated and tested: non-planar and planar. The non-planar sensors have topographic features on the order of 2 μm which complicate such fabrication processes as photolithography, metallization, plasma etch, and ion implantation. These complications are largely absent in the planar devices, which have reduced topography by the application of chemical mechanical polishing.
An important fabrication step in common surface-micromachined processes is the release etch, whereby a sacrificial oxide is etched in an aqueous HF solution to create free standing structures. Ideally there is a high selectivity of the HF etch rates between the sacrificial oxide and structural material. However, since the structural material will etch at a finite rate, there is a danger that the it will be completely removed during a long release etch. To address this problem, work was done to optimize both the chemistry of the etchant and the geometry of the structure. Also, closed form models were developed to describe the behavior of the release etch for a variety of useful geometries.
In order to predict the output of a pressure sensor, it is necessary to understand the mechanical behavior of a micromachined diaphragm. Thin plate, small deflection theory does not accurately predict sensor response. A model based on thick plate, large deflection theory was developed which includes thin film stress effects. This model is a better representation of actual sensor characteristics.
Keywords
MEMS, microelectromechanical systems, pressure sensors, surface micromachining, release etch, built-in stress
Document Type
Dissertation
Language
English
Degree Name
Electrical Engineering
Level of Degree
Doctoral
Department Name
Electrical and Computer Engineering
First Committee Member (Chair)
Don L Kendall
Second Committee Member
Kenneth Jungling
Third Committee Member
Joseph L Cecchi
Fourth Committee Member
James H Smith
Fifth Committee Member
Jeffry J Sniegowski
Recommended Citation
Eaton, William P. IV. "Surface Micromachined Pressure Sensors." (1997). https://digitalrepository.unm.edu/ece_etds/636