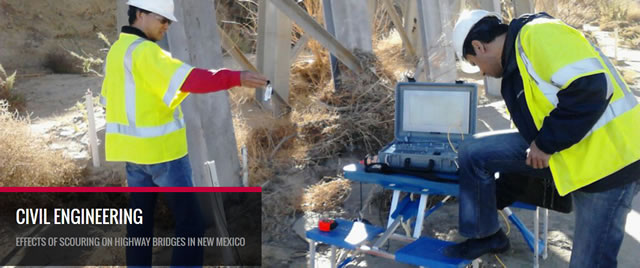
Civil Engineering ETDs
Publication Date
9-3-2013
Abstract
As the use of advanced composite materials continues to grow in the aviation industry, damage detection techniques need to be developed and tested. Impact damage on aluminum aircraft structures can be detected from obvious surface indications. This is not the case in composite aircraft structure. Large interply delaminations and substructure disbonding may occur as a result of an impact, often leaving no visual indications of damage. This research investigates the use of conventional hand-deployed ultrasonic (UT) inspection techniques and more advanced UT pulse-echo and resonance scanning techniques to detect and characterize damage in full-scale carbon fiber fuselage structure. It also examines embedded and bonded methods of deploying an in-situ fiber optic (FO) Swept Wavelength Interferometry (SWI) strain sensing system for damage detection. The hypothesis is that the more advanced scanning nondestructive inspection (NDI) techniques used in the study will more effectively detect and characterize damage modes in the fuselage panels than hand-deployed UT techniques. It is further hypothesized that impact damage created by both simulated hail and steel spherical tip impacts will create a permanent, detectable strain change that can be detected by the FO strain measurement system. Two fuselage panels representative of structures seen on advanced composite transport category aircraft were fabricated. They each measured approximately 56 x 76'. The structural components consisted of a 16 ply skin, co-cured, hat-section stringers, fastened shear ties and frames. The material used to fabricate the panels was T800 unidirectional, carbon pre-preg and was processed in an autoclave. Simulated hail impact testing was conducted on the panels using a high velocity gas gun with 2.4' diameter ice balls. The ice impact tests were performed in collaboration with the University of California San Diego (UCSD). In addition to the simulated hail impact testing, 2' diameter spherical tip steel impacts were conducted to simulate impact damage introduced during heavy ground maintenance operations. The extent of 16 ply skin damage induced on the panels ranged from less than 1 in2 to 55 in2 of interply delamination. Substructure damage on the panels included shear tie cracking, delamination of the built-up pad sections behind the fastened shear ties, and stringer-to-flange disbonding. Substructure damage away from the site of high energy ice impacts was often not detected with hand-deployed UT, which can be attributed to failure to inspect far enough away from the impact site. This additional damage was detected using the more advanced scanning techniques. Data collection from the embedded FO was not possible due to light attenuation caused by micro-bending induced in the fiber. It was determined that increasing both the numerical aperture of the FO and the diameter, in combination with adjusting the layout orientation used, may make it possible to measure strain change using this technique. Detectable strain indications were obtained using the backside bonded FO in 15 of the 25 interrogated steel tip impacts. Increasing the robustness of this deployment method could provide a means for in-situ damage detection.'
Keywords
Carbon fiber-reinforced plastics--Fatigue--Measurement, Airplanes--Fuselage--Materials--Fatigue--Measurement, Impact--Measurement.
Sponsors
Federal Aviation Administration - William J. Hughes Technical Center
Document Type
Thesis
Language
English
Degree Name
Civil Engineering
Level of Degree
Masters
Department Name
Civil Engineering
First Committee Member (Chair)
Maji, Arup
Second Committee Member
Ross, Timothy
Recommended Citation
Neidigk, Stephen. "Detection and characterization of impact damage in carbon fiber aircraft fuselage structure." (2013). https://digitalrepository.unm.edu/ce_etds/76