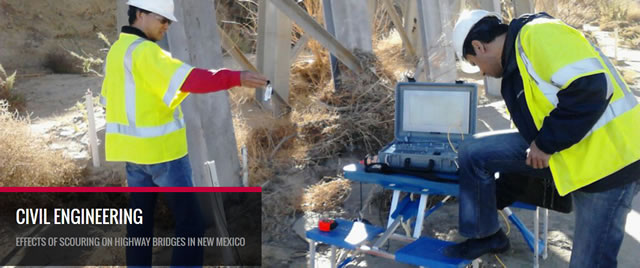
Civil Engineering ETDs
Publication Date
9-10-2010
Abstract
Bi-axial testing of composite structures has been an important topic in the research community for some years now. Bi-axial test specimens in the past have typically been cruciform specimens with a tapered thickness gage section. This ensures that the specimen will fail under bi-axial loading rather than uni-axial loading due to high stress concentrations at the intersecting loading arms. To reduce the stress concentration in the loading arms the intersection points are rounded and curved inward toward the center of the specimen. By having the curvature of the intersecting arms come closer into the specimen it reduces the amount of uni-axial stress at that point. In order to reduce the stress even more, tapered thickness gage section milling is required to achieve adequate bi-axial failure. In the proposed research these specimens will be modified so that no milling of the gage section is required. The process of milling the gage section of the composite laminate could inflict initial damage to the specimen which would yield inaccurate results. The modified bi-axial specimen will instead have aluminum shims bonded to the rounded corner to ensure bi-axial failure. The location of the shims was determined using Finite Element Analyses which verified the location and magnitude of the stress concentrations. The use of the aluminum shims could allow the cruciform specimen to be completely unscathed of any initial damage. The specimens are thick woven carbon fiber/epoxy bi-axial specimens which previously havent been tested before. Two types of geometries were fabricated, one out of IM7/UF3352 and one out of IM7/PATZ materials, both with a [(0/90)]s lay-up. The first geometry had the aluminum shims. The second configuration consisted of a smaller composite laminate sandwiched in between two pre-fabricated G10 glass/epoxy panels and only machining away the G10 material, keeping the composite laminate unscathed. Both geometries had tapered thickness gage section counterparts for comparison purposes. The shimmed design showed undesirable failure modes but provided a reliable lower bound for bi-axial strength design. The sandwich panel design showed ideal failure conditions for all tests. This shows that a modified bi-axial composite specimen can be developed that limits the amount of machining and can still produce accurate results. Additional tests were conducted to study the effect of stress concentrations around holes of different diameter under biaxial load. Results were interpreted with the aid of Finite Element Analyses.'
Keywords
Fibrous composites--Testing, Materials--Dynamic testing, Finite element method.
Sponsors
New Mexico Alliance for Minority Participation Bridge to the Doctorate, Air Force Research Laboratory Space Vehicles Directorate.
Document Type
Thesis
Language
English
Degree Name
Civil Engineering
Level of Degree
Masters
Department Name
Civil Engineering
First Committee Member (Chair)
Tarefder, Rafi
Second Committee Member
Dumm, Hans Peter
Recommended Citation
Torres, Anthony. "The development of a modified biaxial composite test specimen." (2010). https://digitalrepository.unm.edu/ce_etds/35