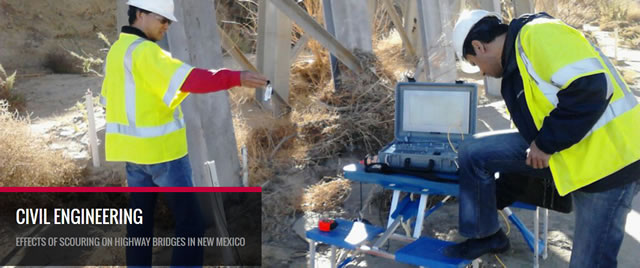
Civil Engineering ETDs
Publication Date
Spring 4-15-2021
Abstract
Nonlinearities exist in all real-life systems and can be caused by behaviors such as large deformations, yielding, contact, etc. which can result in phenomena not found in linear testing. Considering nonlinear behavior in dynamic analyses can be beneficial to increase model predictability and can accurately characterize system responses. Generally, accelerometers are commonly used in linear and nonlinear vibration testing to obtain the acceleration response of a system. However, some systems may render the use of accelerometers problematic, or accelerometers may introduce limitations to measurement capabilities such that it can be beneficial to obtain experimental data using different sensors. In the context of experimental data, strain gauges can alternatively be used to obtain dynamic properties both in the laboratory and in the field. Strain gauges are additionally capable of quantifying damage that is directly estimated from strain measurements, such as stresses, that accelerometers cannot obtain. But, measuring strain in structural dynamics can be disincentivizing and expensive due to the complexity of data acquisition, lack of portability, high costs, and the requirement of prior knowledge and training required for a proper installation. The purpose of this research is to introduce an alternative resource to measure nonlinear dynamics of structures using strain in a cost-effective and streamlined platform. This thesis accomplishes the goal of developing and testing a low-cost, efficient, wireless, intelligent sensor for strain (LEWIS-S) for the nonlinear dynamic assessment of a simple structure. The LEWIS-S sensor functions on a platform of various Arduino hardware components and free Integrate Development Environment (IDE) software. Two different sensor configurations were used in the validation testing in this research, namely, a uniaxial friction-magnetic strain checker and a traditional pasted uniaxial strain gauge. Static and dynamic validation tests were conducted on a small cantilever beam where the LEWIS-S was compared to a commercial DAQ system to verify the accuracy and dependability of the sensor. The LEWIS-S sensor was then used in nonlinear dynamics tests to experimentally characterize the softening behavior of a cantilever beam with geometric and inertial nonlinearities produced by large deformations. Two experiments were performed on a nonlinear cantilever beam with measurements obtained at the base with the LEWIS-S sensor and at the tip using an accelerometer. The first test was a sine sweep through the fundamental resonance of the system and the second test was a ring-down from an initial static deformation. Based on the results of the validation and nonlinear experimental testing, the LEWIS-S sensor demonstrated various streamlined sensing capabilities. Namely, the sensor is approximately 95% cheaper than standard commercial equipment and the compact design reduces the plan-view-footprint of the equipment by approximately 75%. Furthermore, the small footprint and wireless function enhances the portability which increase sensing capabilities. The versatility of the sensor also allows for the compatibility of different strain gauge attachments which can be useful for sensing optimization during testing. Additionally, the LEWIS-S has an inherently simple design such that limited knowledge is required to manually assemble and use the sensor. Future research proposes deploying the LEWIS-S in field testing as well as advancing the performance of the LEWIS-S by addressing sensor limitations.
Keywords
Strain Sensors, Low-Cost Sensors, Nonlinear Dynamics
Document Type
Thesis
Language
English
Degree Name
Civil Engineering
Level of Degree
Masters
Department Name
Civil Engineering
First Committee Member (Chair)
Dr. Fernando Moreu
Second Committee Member
Dr. Robert Kuether
Third Committee Member
Dr. Rafiqul Tarefder
Recommended Citation
Robbins, Eric. "Development of a Low-cost Efficient Wireless Intelligent Sensor for Strain (LEWIS-S) and Applications in Measuring Nonlinear Dynamics." (2021). https://digitalrepository.unm.edu/ce_etds/285
certificate-final-elect1pdf.pdf (180 kB)
info-cover.pdf (130 kB)
Embargo Payment Receipt.pdf (209 kB)
Embargo Request Reason.pdf (89 kB)