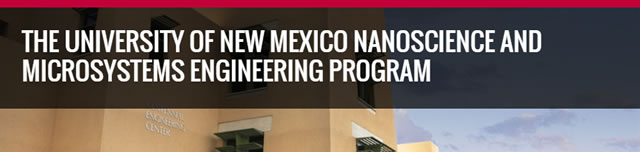
Nanoscience and Microsystems ETDs
Publication Date
Fall 11-30-2022
Abstract
Metal additive manufacturing (AM) is a disruptive technology enabling the fabrication of complex and near-net-shaped parts by adding material layer-wise. It offers reduced lead production time. AM processes are finding applications in many industrial sectors such as aerospace, automotive, biomedical, and mold tooling. Despite the tremendous advantages of AM, some challenges still prevent this technology's adoption in high-standard applications. Anisotropy and inhomogeneity in the mechanical properties of the as-built parts and the existence of pores and lack-of-fusion defects are considered the main issues in directed energy deposition (L-DED) parts. Laser-engineered net shaping LENS® offers excellent possibilities to fabricate metal tools with complex geometry, but there are limitations regarding some materials. AISI 420 martensitic steel, an alloy with a useful combination of high strength, hardness, and corrosion resistance, is an example of one such material where few laser-directed energy deposition L-DED investigations have emerged. The Martensitic 420 stainless steel was successfully fabricated using the LENS® technique with high relative density from Nitrogen gas-atomized spherical powder in two different environments on preheated 190⁰C 316L substrate. The microstructure of LENS® deposited 420 steel consisted of retained austenite, submicron martensitic laths, and carbides at grain boundaries.
Microstructure and phase composition were characterized using scanning electron microscopy and X-ray diffraction. Java-based Materials Properties JMAT pro software was used to identify the phase fractions concerning temperature with equilibrium conditions. The microhardness of the deposited sample is 663±13HV which is comparatively higher than the conventional 420 steel. The stress at failure was approximately 803.53 MPa, and the strain was 3% of as-deposited sample. The fracture surface of as-built 420 shows fewer dimples as an indication of the less ductile mode of fracture and observed secondary crack propagated through the grain boundary inside the microstructure. Post-deposition heat treatments were employed to improve mechanical properties and optimize the microstructure. The maximum tensile strength was 1410 MPa, with ductility increased four times (total elongation of 20%) of the as-quenched sample than the as-deposited 420 martensitic steel. A Hall-Petch relationship describes the link between relevant grain dimension and yield strength. In addition, the martensitic 420 steel was deposited on preheated 110 ⁰C and no preheated 316L substrate by L-DED technique to compare the microstructure and mechanical properties.
Keywords
Martensitic steel, Additive manufacturing, Directed energy deposition, Heat treatment, Laser engineered net shaping, Mechanical Properties
Document Type
Dissertation
Language
English
Degree Name
Nanoscience and Microsystems
Level of Degree
Doctoral
Department Name
Nanoscience and Microsystems
First Committee Member (Chair)
Osman Anderoglu
Second Committee Member
Yu-Lin Shen
Third Committee Member
Tariq A. Khraishi
Fourth Committee Member
Pankaj Kumar
Recommended Citation
Hassan, Md Mehadi. "Characterization of materials properties in Additively Manufactured AISI-420 martensitic steel deposited by Laser engineered net shaping." (2022). https://digitalrepository.unm.edu/nsms_etds/69